As plant managers, maintenance experts, and engineering professionals, we know the backbone of any operation involving temperature-sensitive goods is its refrigeration system. It’s not just about getting and keeping products cold; it’s about efficiency, and reliability. Regular maintenance can account for 12 to 18% return annually in the form of energy savings. Not only that, according to Doug Biedenweg, an industrial process engineer, for every $1 dollar in maintenance deferred you will pay $4 in capital renewal costs when that equipment fails. That seems to make sense right? If so, don’t defer the critical maintenance that will make those savings reality.
Optimizing Operational Efficiency
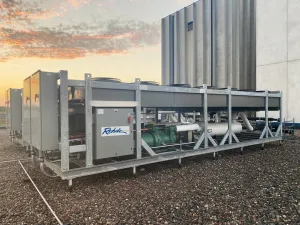
In any industrial setting, operational efficiency is the cornerstone of performance and profitability.
A well-maintained refrigeration system is synonymous with optimized operational efficiency. For example, keeping coils clean and belts properly tensioned can ensure that heat transfer is always optimized. When heat transfer isn’t optimized, equipment runs longer, resulting in the use of more energy for the same amount of work. And we all know what that means: higher operational costs to the tune of 12 to 18%, and a reduced bottom line. Preventative maintenance ensures that every component is optimized, thus minimizing energy draw and the resulting operating costs.
Friction is the enemy of energy efficiency, most people agree on that, but so many times we see equipment that isn’t lubricated properly, and the compressors or fans have failed in a way that could have been avoided.
Maximizing Equipment Lifespan

From an asset management perspective, the longevity of your refrigeration system is paramount. Regular maintenance is not just about preventing breakdowns; it’s about extending the life expectancy of your equipment. When you inspect your equipment regularly you can monitor and remove debris which may be hiding an issue. Each maintenance session is an opportunity to catch early signs of wear and to replace parts before they fail. This is essential for planning capital expenditures and avoiding the financial burden of a plant shutdown. According to statistics, using critical equipment to failure costs as much as 10 times more than the maintenance program that would have prevented it. The larger the operation, the more expensive downtime becomes, in some cases costing hundreds of thousands to perhaps a million dollars per hour.
Guaranteeing Product Integrity
Product quality is non-negotiable, and a lapse in refrigeration can be catastrophic. Downtime in a cheese storage facility, for example, can be catastrophic. You spend money on the latest control systems that keep your temperatures optimal 24/7, however, downtime due to lack of maintenance can render those controls useless. Product recalls will result in lost revenue and could easily damage your reputation. Maintaining a constant temperature can be critical to your product’s flavor development, ageing, and freshness.
Minimizing Downtime Risks
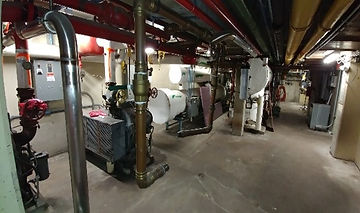
Downtime is a threat to productivity and profitability. An unexpected failure can halt production lines, lead to inventory losses, and spoilage which can affect delivery schedules. Regular maintenance helps to prevent these scenarios by ensuring that potential issues are addressed before they lead to system failure.
If you’re inspecting your equipment and fixing repairs, you may be able to go for very long periods of time with no downtime. Time is money.
Prioritizing Workplace Safety
In the world of industrial refrigeration, a system failure isn’t just an operational issue—it’s a safety concern. While ammonia is typically safer than halocarbon-based refrigerants, leaks of refrigerants, such as ammonia, or halocarbons, can be hazardous. For example, ASHRAE has a classification system, and that’s an article that we don’t have the time for in this article. ASHRAE provides that a letter and number are issued to refrigerants based on their toxicity and flammability. Understanding that halocarbons are typically more flammable and with propane, ethylene, and butane in their names you quickly make the connection. The big thing to remember is maintenance is critical for the safety of the plant personnel regardless of the type of refrigerant. It’s our duty to maintain a safe working environment, and regular system inspections are a cornerstone of this commitment.
Facilitating Financial Forecasting

Effective maintenance regimes allow for predictable financial forecasting. By having a maintenance schedule, you can plan for the associated costs in your operational budget. This forward planning reduces the risk of financial surprises associated with emergency repairs and system downtime.
Predictive or preventative? Once you understand the optimal maintenance patterns for your equipment you can look at predictive maintenance as an added layer of financial forecasting and potential savings. Predictive maintenance on industrial refrigeration systems can save as much as 40% in terms of costs over reactive, and 8-12% over preventative maintenance. Why? Because adding maintenance when your equipment needs it most is optimization in the most fundamental sense.
In conclusion, the message is clear: ignoring industrial refrigeration maintenance is a risk you cannot afford. It is your responsibility to ensure that your refrigeration systems are not just functioning but are performing efficiently, safely, and in compliance with all regulations. So, it pays to prioritize maintenance, not just as a routine task, but as a strategic imperative for the success of your operations.
Keep the gears turning, the products chilled, and the operations flowing.
Rohde Brothers, Inc. has experience in designing, installing, controlling, and maintaining industrial refrigeration systems. To schedule a maintenance inspection, reach out to Service Manager, Mike Kruschke at 920-893-5905 today!