Northstar Glycol Chiller
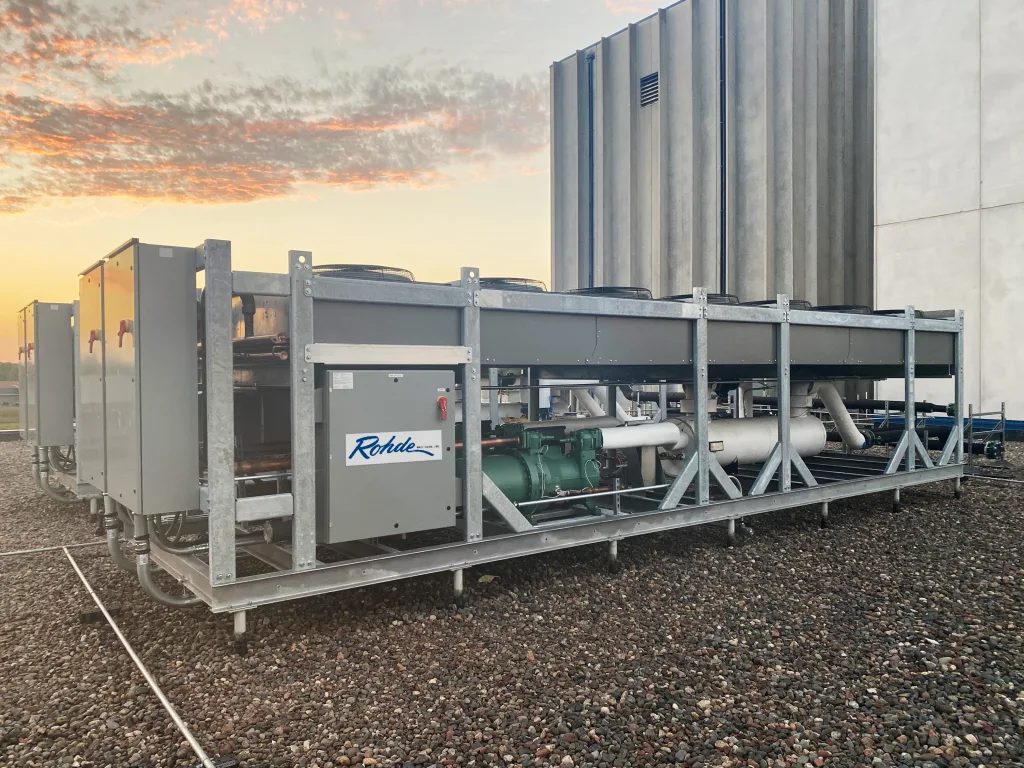
Rohde Brothers, Engineered Solution
- Chiller Configuration: Design and installation of two dual circuit chiller skids, each providing 170 tons of refrigeration to produce 425 gpm of 30°F chilled glycol.
- Compressors: Each skid includes two 85-ton sliding-vane screw compressors, powered by 140 HP motors.
- Evaporators: Two shell and tube evaporators per skid.
- Condensers: Two fan-cooled condensers per skid, with seven 30-inch fans per circuit, designed for 86°F ambient conditions.
- Expansion Valves: Installation of two electric expansion valves per skid.
- Economizers: Two economizers per skid.
- Refrigerant: R134a refrigerant charge for each chiller skid.
- Piping and Insulation: All copper piping with a combination of closed-cell PE and fiberglass insulation, aluminum jacketed.
- Chilled Glycol System:
- Glycol Surge Tank: A 2,000-gallon HDPE glycol surge tank, insulated with urethane closed-cell foam with headers to stratify the tank with cold supply glycol on the bottom and warm return glycol on the top.
- Circulation Pumps: Two dehumidifier glycol circulation pumps, each with a capacity of 425 gpm and 70’ TDH.
- Chiller Pumps: Two glycol chiller circulation pumps, each with a capacity of 275 gpm and 30’ TDH.
- Controls:
- Sensors and Wiring: Installation of pressure, flow, and temperature sensors, along with necessary control wiring.
- Control Hardware: Allen-Bradley PLC and HMI hardware, including associated programming.
- Motor Control Panel: UL-listed motor control panel with power wiring.
- Fan Programming: Implementation of staged condenser fan programming for efficient operation.
- VFD Controllers: Integration of Variable Frequency Drive (VFD) pump controllers for precise flow control.
- Process Trending: Real-time process trending for monitoring and optimization.
- Remote Monitoring: Enabling remote monitoring capabilities via an internet connection.
- New corrosion resistant PVC piping and valves.
Northstar Processing Chilled Glycol Project
In Litchfield, MN, Revela Foods (previously Northstar Processing) utilizes a spray drying facility to provide product drying services to food manufacturers. Many of the products being dried are sticky and difficult to dry in the summer due to the humidity. To address these issues, Revela Foods contracted Caloris Engineering LLC to add an inlet air dehumidification unit to the Dryer.
Caloris ran into project delivery complications because of extremely long lead times, more than 52 weeks, for glycol chilling equipment sourced from the common brand name suppliers. Without a new solution, Revela Foods would miss an entire summer drying season waiting on the chiller delivery.
Enter Rohde Brothers, Inc.! Rohde was able to manufacture and deliver a state-of-the-art chilled glycol system for Revela Food’s spray drying facility, in just weeks. The project involved the design, fabrication, and installation of multiple dual-circuit chiller skids, glycol circulation pumps, and advanced control systems to ensure optimal performance and reliability.
The roof-mounted chiller system featured two 170-ton chiller skids, using four sliding-vane screw compressors, economizers, and fan-cooled condensers, all controlled by Allen-Bradley PLC and HMI hardware. The design included a redundant chiller circuit and the ability to expand for the future addition of Spray Dryer #1. This high-efficiency system included high turndown capabilities and low ambient controls allowing for effective operation over a wide range of conditions.
The roof-mounted chilled glycol system featured a decoupled system. This system employs independent glycol pumps to circulate glycol to the chillers, as well as glycol pumps to circulate to the dehumidification equipment. Fused and insulated high density polyethylene (HDPE) piping connected the 1,500-gallon insulated polyethylene surge tank to both the chillers and the dehumidification equipment. The entire system was filled with 30% propylene glycol.
Because of Rohde’s planning and on-time execution, Revela Foods was up and running, just in time for their 2023 summer drying season!