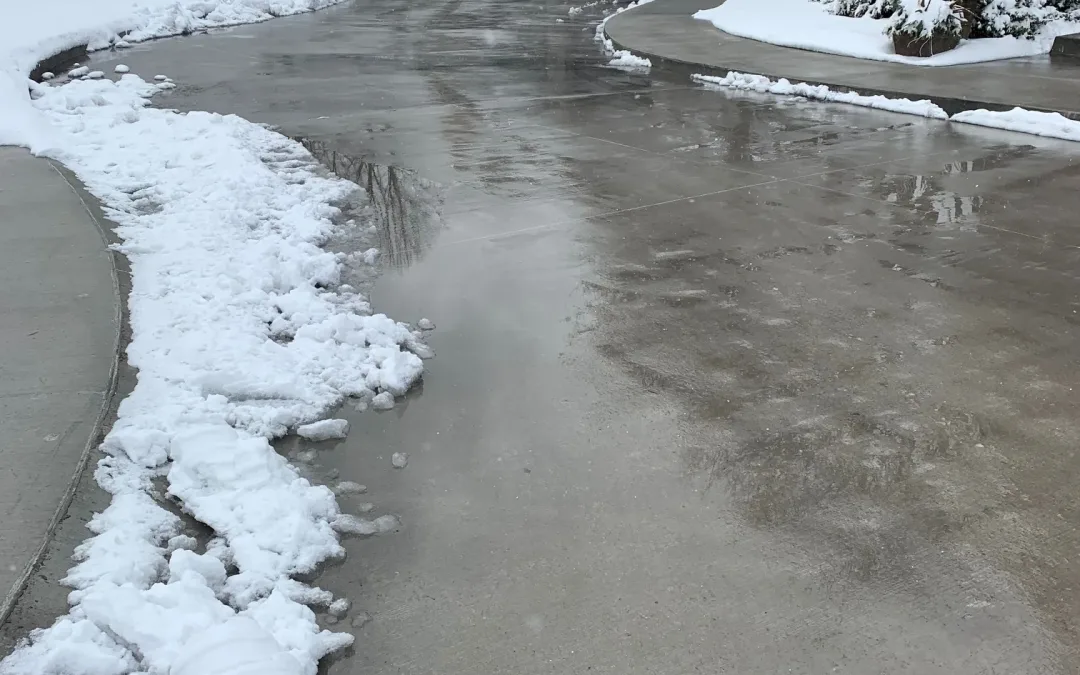
Redefining Winter Comfort: Rohde’s Innovative Snow Melt System for a Boutique Hotel
The Challenge: Faced with the need to provide a safe, snow-free environment for guests, the boutique hotel sought a solution that could handle a large and varied outdoor area. This challenge called for a design that was both innovative and aggressive.
Praise from Industry Experts: Rick Nierzwicki, Managing Director at CG Schmidt, commended the project as one of the most aggressive design solutions for such a vast area. He emphasized the success of the project was largely due to Rohde’s meticulous attention to detail and commitment to a tight construction schedule.
Our Customized Solution:
- Extensive Snow Melt System: We designed and installed a 70,000 square foot in-slab snow melt system covering the entire parking structure, including decks, drives, sidewalks, stairwells, and ramps. The system comprised 25 zones and over 22 miles of PEX tubing.
- Advanced Equipment Installation: We furnished and installed key components like steam to hot water heat exchangers, pumps, hydronic equipment, in-slab tubing, and controls.
- High-End Technical Components: The project included a 3-stage high-pressure steam reducing station, two steam to hot water heat exchangers, hot water pumps, an expansion tank, glycol fill system, and sophisticated snow melt controls.
- Storm Water Drainage Enhancement: We added and modified the storm water drainage system for the parking deck to complement the snow melt system.
- Ventilation System Upgrade: The parking structure’s ventilation equipment was replaced with new fans and controls, ensuring proper ventilation to prevent carbon monoxide buildup.
Conclusion: This innovative snow melt system stands as a testament to Rohde’s engineering prowess and dedication to client satisfaction. By ensuring a safe, snow-free environment, we enhanced the guest experience while safeguarding the hotel’s infrastructure. If your business is looking for groundbreaking solutions in heating and ventilation, Rohde Brothers is your go-to partner.