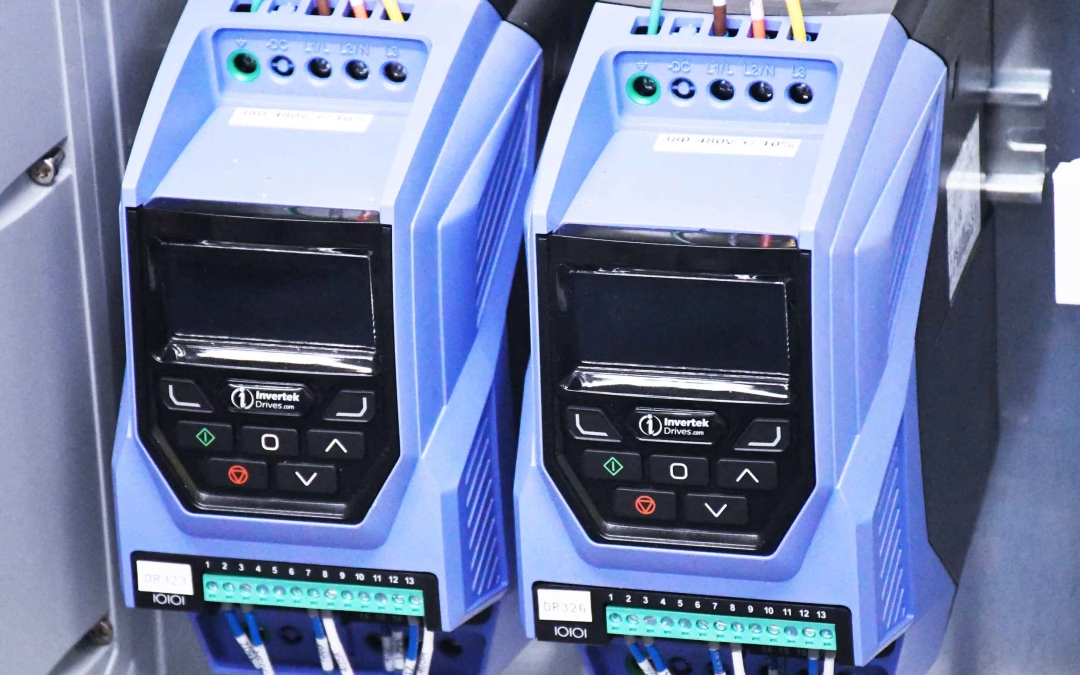
How Variable Frequency Drives Can Save Your Company Money in the Long Term
In manufacturing, every watt counts, and downtime is the enemy of profit. The spotlight is typically fixed on efficiency, reliability, and safety. As we prepare for marketplace volatility, these factors become even more critical. Variable Frequency Drives (VFDs) have emerged as a game-changing technology in this regard, offering significant cost savings and operational efficiencies. Here’s how VFDs can help your company weather financial highs and lows and contribute to a solid financial position.
First, what is a VFD? A VFD is a motor speed controller that works by modulating the frequency of the electricity being supplied to an electric motor. This motor could be driving pumps, it could be driving fans, or it could be applying physical pressure to something.
VFD is not the motor and for general understanding fixed speed systems are just that, fixed speed and lacking a digital controller, mostly these motors are attached to a gearbox or some other kind of damper, or valve that would control the output.
VFDs.com has a calculator to find an approximate savings based on the following. It should be noted that no calculator can be 100% accurate because there are many factors involved in individual applications that are not the same.
The formula for predicting the savings in energy cost is fixed and it requires you to understand some things. The basis of this analysis is a 10hp pump with a VFD operating at 70% speed 168 hours per week with 5 days of downtime annually.
The results of the analysis are as follows: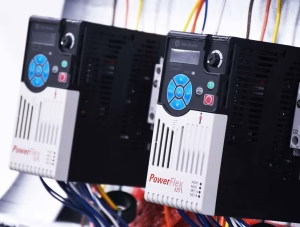
- Number of motor run hours – 8760 hours annually
- Percent of that time the motor will run at 95% of the time @70% power
- Motor Horsepower (HPx.746-Kilowatts)
- The utility rates $.09/KWH
- Motor Efficiency
- VFD Cost assumption: $2000
- Installation and downtime costs (variable, not included in this analysis)
- Possible incentives or rebates on efficiency and equipment (also varied and not included for simplicity)
The savings are typical and repeatable:
- Estimated annual operating cost without VFD: $8616
- Estimated annual operating cost with VFD: $1856
- The annual cost savings: $6760
- Payback time: 8.46 Months
Reduced Energy Consumption
One of the most compelling benefits of VFDs is their ability to cut energy costs, which can be more than 40% of the total cost of ownership. Unlike traditional AC motors that run at constant speed, VFDs adjust the motor speed to match the actual demand. This means:
- Energy Savings: By optimizing motor speed, VFDs applied to pumps or fans can reduce energy consumption by up to 50%. This leads to substantial savings on electricity bills, which is often one of the largest operational expenses in manufacturing. Another factor that will save energy is the VFD can start a process more efficiently by ramping up the equipment more slowly than an on/off switch.
- Reduced Carbon Footprint: Lower energy consumption translates to reduced greenhouse gas emissions, helping companies meet sustainability goals and avoid potential penalties.
Extended Equipment Lifespan
VFDs not only save energy but also extend the lifespan of your equipment:
- Soft Starts and Stops: VFDs enable soft starts and stop, reducing mechanical stress on motors and other components. The in-rush of current during start up of a static motor can be 600% while VFD’s typically max out at 150%. This minimizes wear and tear, leading to fewer breakdowns and longer equipment life.
- Reduced Maintenance Costs: With fewer mechanical stresses and smoother operation, maintenance needs decrease, resulting in increased bearing life, lower maintenance costs and less frequent equipment replacement.
Increased Process Control and Efficiency
Enhanced control over manufacturing processes can lead to significant savings:
- Precision Control: VFDs provide precise control over motor speed, allowing for more accurate process management. This reduces waste and increases the energy efficiency of production lines and supporting utilities.
- Adaptive Operations: VFDs can adapt to varying load conditions, ensuring optimal performance and efficiency at all times. This adaptability reduces the need for manual adjustments and oversight, saving labor costs.
- Automation: VFDs can be integrated with your distributed process control systems to increase reliability and reduce variability.
Enhanced Safety Features
Safety is paramount in manufacturing, and VFDs contribute to safer work environments:
- Integrated Safety Mechanisms: VFDs come with built-in safety features such as motor and load protection, fault detection, and emergency-stop functionalities. These features prevent accidents and equipment damage, reducing liability and associated costs.
Conclusion
In an economic downturn, maximizing efficiency and minimizing costs become critical for manufacturing companies. Variable Frequency Drives (VFDs) offer a compelling solution by reducing energy consumption, extending equipment life, enhancing process control, improving reliability, and ensuring safety.
At Rohde Brothers, Inc., we understand the challenges manufacturers face and are committed to helping you build a more efficient and resilient operation. Let’s build something together and navigate the future with confidence.