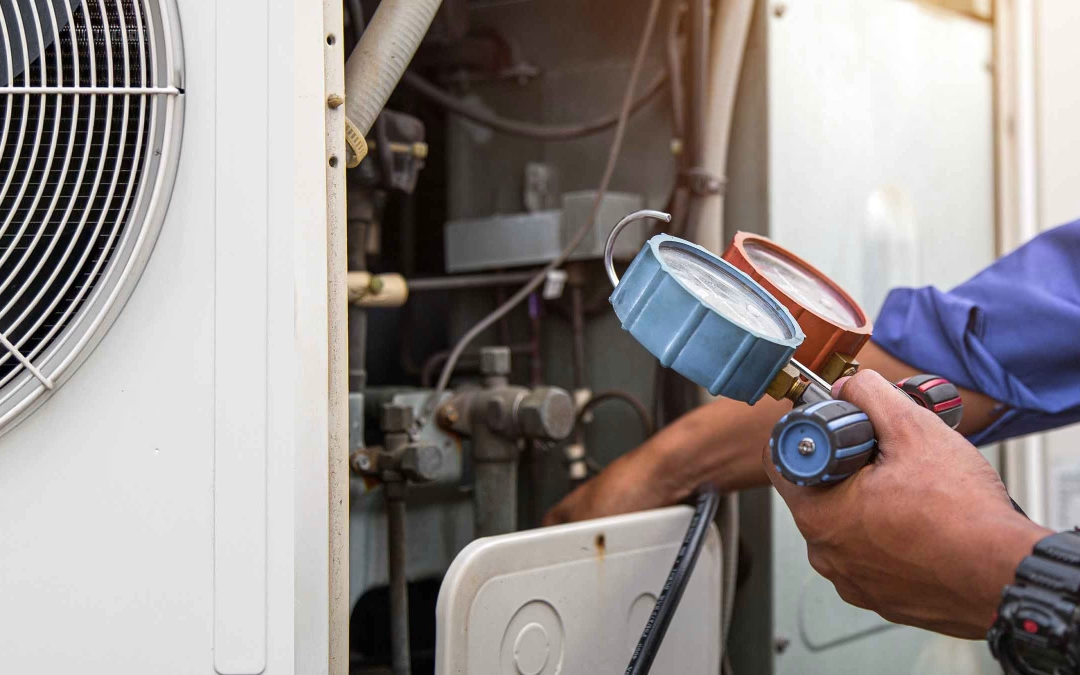
Optimizing HVAC Systems for Food Manufacturing Facilities
Maintaining precise environmental conditions is not just a preference. In fact, in food processing, it’s a necessity. From preserving product quality to meeting strict food safety standards, HVAC systems play a critical role in ensuring temperature control, air quality, and energy efficiency. Let’s explore how food manufacturers can optimize their HVAC systems to achieve these goals while staying compliant with food safety standards.
Why HVAC Matters in Food Manufacturing
Food manufacturing facilities face unique challenges every day. The need to control temperature, humidity, and airborne contaminants in production and cold storage is paramount for several reasons:
Preserving Product Quality: Temperature and humidity levels may impact the product flavor, mouth feel, and other attributes. Fluctuations can compromise food integrity, texture, and shelf life.
Ensuring Food Safety Compliance: standards, such as those set by the FDA and USDA, demand strict environmental controls to prevent contamination.
Worker Comfort and Productivity: Stable air quality and temperature improve working conditions for employees.
Energy Costs: HVAC systems account for a significant portion of a facility’s energy use. Efficient systems can drastically reduce costs. The use of waste heat to control office and/or production temperature in winter months can save thousands of dollars each year.
When you don’t have control over your indoor air, you will not have control over product quality or freshness.
Optimizing HVAC Systems: Key Strategies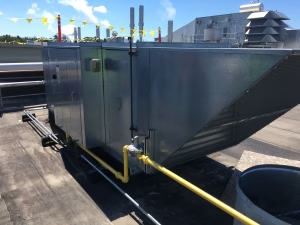
Prioritize Temperature and Humidity Control Systems
Zoned HVAC Systems: Divide your facility into zones based on specific temperature, pressure, and humidity requirements. . Zoned systems allow you to tailor settings based on operational requirements of the facility, ensuring the best possible conditions in each space without overworking the system.
Real-Time Monitoring: Install advanced sensors to track temperature and humidity in real-time. Automated alerts can help identify and correct issues before they impact production. A digital interface can be developed that allows readings to be viewed and adjusted at-a-glance.
Enhance Air Filtration and Ventilation
High-Efficiency Filters: Use HEPA or ULPA filters to capture airborne particles and contaminants, protecting both products and workers.
Positive and Negative Air Pressure Zones: Maintain positive pressure in clean areas to prevent contaminants from entering, and negative pressure in waste or processing areas to contain odors and debris.
Air Turnover: Make up air is required to provide a continuous flow of fresh air into the facility to maintain air quality and remove contamination. ASHRAE standards recommend minimum outside air exchanges based on the occupancy of the space. It is often beneficial to increase the amount of fresh air exchange.
Boost Energy Efficiency
Upgrade Equipment: Use Variable Frequency Drives (VFD’s) to control fans and pumps to conserve energy. Consider high-efficiency HVAC units and geothermal systems, which adapt to changing heating and cooling needs conserving energy in the process.
Preventive Maintenance: Regularly clean ducts and filters, inspect refrigerant levels, and replace worn belts, motors, and actuators (dampers) to keep systems running efficiently.
Energy Recovery Ventilators (ERVs): Recover waste heat, humidity or cooling from exhaust air and push that heat to office or production areas to reduce energy consumption.
Room Cleaning Cycles: At certain times when facilities are undergoing cleaning with hot water, cycling the space with 100% outside air will more efficiently remove the excess humidity and heat and require less overall maintenance.
Meet Sanitary Standards with Specialized Design
Smooth Surfaces: Ensure HVAC components, such as ducts and vents, are made from easy-to-clean stainless-steel materials and properly sloped to avoid ponding and contamination buildup.
Condensation Control: Prevent moisture buildup on HVAC surfaces with proper insulation and drainage to block mold and bacteria growth.
Regulatory Compliance: Partner with Rohde Brothers, Inc. HVAC specialists who understand food manufacturing standards, such as FSMA, and design systems to meet these strict guidelines.
Incorporate Smart Controls
Integrated Building Management Systems (BMS): Centralize HVAC controls to adjust settings based on production schedules and occupancy levels, reducing unnecessary energy use.
Predictive Analytics: Use data driven tools to forecast HVAC demand based on historical data, weather patterns, and production schedules.
Benefits of Optimized HVAC Systems
HVAC can make up 40-60% of overall energy consumption in a food manufacturing facility. By optimizing HVAC systems, food manufacturers can realize several advantages:
Cost Savings: Energy-efficient systems lower utility bills because they use up to 30% less energy and reduce maintenance expenses.
Regulatory Compliance: A well-maintained HVAC system ensures adherence to food safety and sanitary standards. Experts like Rohde Brothers guide facilities leaders on changes to these standards and how to most effectively comply with them.
Improved Product Quality: Precise temperature and air quality control help maintain the integrity of food products. This positively impacts the business in many ways including sales, marketing, quality, traceability and so on.
Sustainability Goals: Reduced energy consumption contributes to environmental sustainability efforts. These efforts save money and time in the long run.