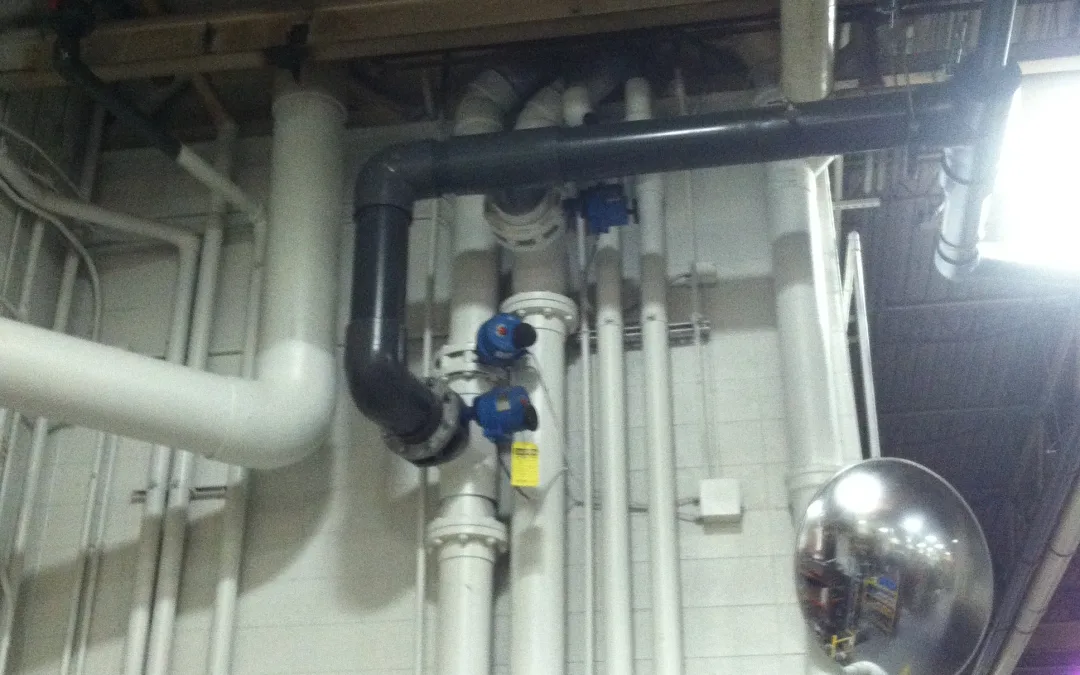
Mercury Marine’s Process Utility Piping Project: A Dual Award-Winning Achievement
At Rohde Brothers, Inc., we’re proud to have completed a pivotal project for Mercury Marine that won both the ABC Project of Distinction and the AGC Build Wisconsin Award in 2017. This project involved comprehensive design/build HVAC and process mechanical services for a die cast addition, along with a complete rebuild of the process piping infrastructure.
The Challenge: Mercury Marine needed to modernize and expand its die casting operations. This required not only an addition to their existing facilities but also a significant overhaul of their process piping infrastructure, all while keeping the plant fully operational.
Strategic Phased Execution: The project was executed over multiple years in phases to ensure there was no disruption to ongoing plant operations. Our team worked meticulously to integrate new systems without affecting the plant’s productivity.
Client Praise: Stephen Mlinaz, Senior Facilities Manager at Mercury Marine, lauded Rohde Brothers for providing comprehensive mechanical system integration packages. He emphasized our contribution in reducing both installation and operational costs while enhancing the original performance expectations.
Customized Solutions:
- Complex Piping Installation: The installation of new piping in highly congested utility tunnels required careful planning and precise execution.
- Utility Piping Replacement: Alongside the cooling water piping, we replaced and upgraded the utility piping in the tunnels.
- Comprehensive Process Utility Modifications: This included alterations to potable water, non-potable water, compressed air, die lube, and wastewater systems.
- Future-Ready Design: Modifications were made with a focus on allowing future expansion of the die casting operations.
Conclusion: This project is a testament to Rohde Brothers’ expertise in managing complex industrial projects that require a high degree of precision and strategic planning. Our work at Mercury Marine not only met but exceeded client expectations, reducing costs and enhancing system performance. For businesses seeking a partner to undertake comprehensive mechanical system upgrades with minimal disruption, Rohde Brothers stands ready to deliver excellence.